High-tech factory for e-car batteries opened in Biberist-Switzerland becomes recycling pioneer
In Biberist So the Libec company opened the first recycling facility for Switzerland's e-car batteries. Thousands of tons of critical raw materials get back into the circulation and save resources.
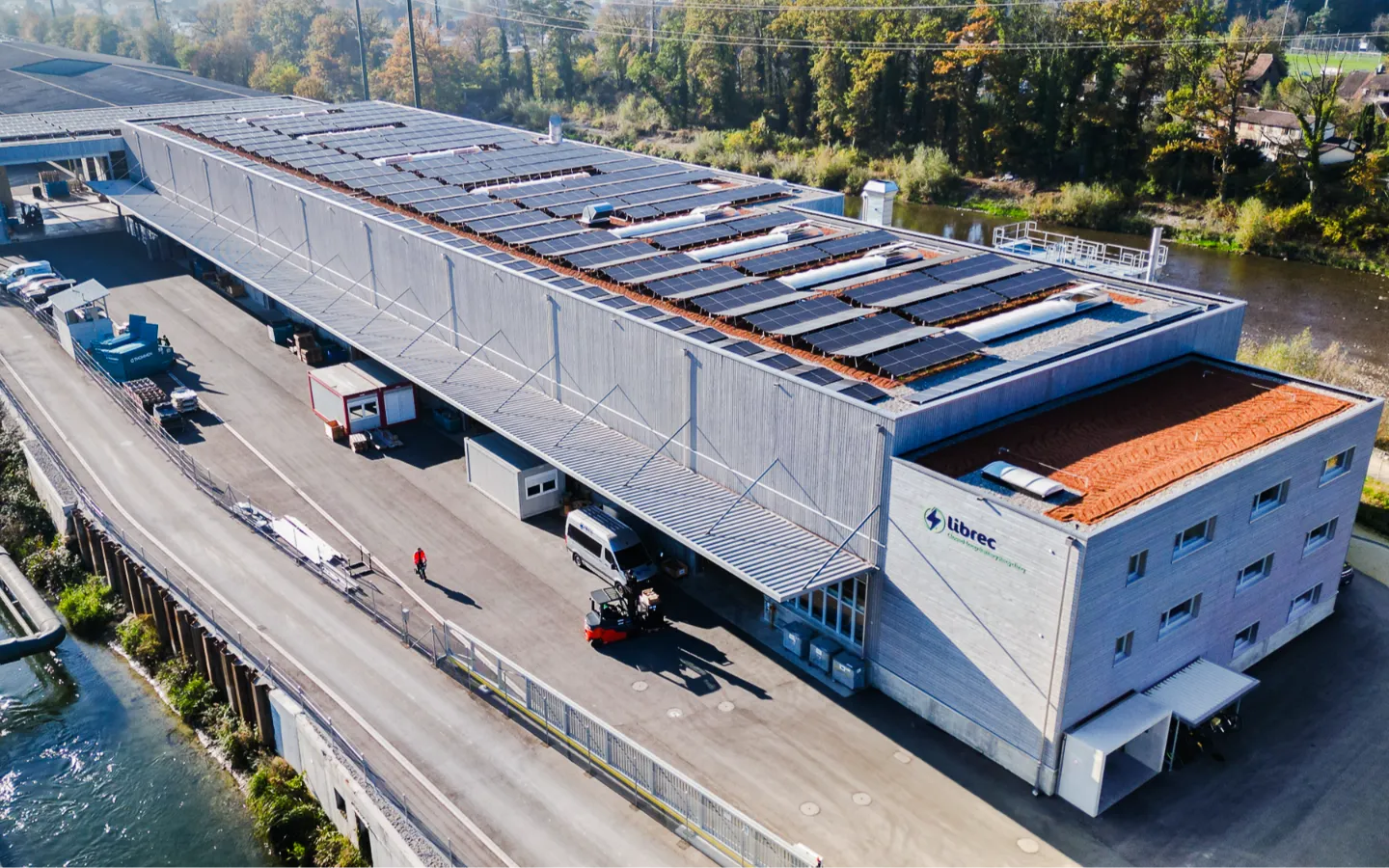
View from April 2025 - Hightech recycling in Biberist: Third life for e-car batteries-Blick
The kitchen table of the Reinhardt family plays a central role in the history of the Libec company. There, today's CEO Jodok Reinhardt discussed with his wife in 2019 how the lithium-ion batteries of the electric cars that were hardly widespread at that time could be recycled. «There are tons of critical and valuable raw materials in a battery. Always getting them out of the earth makes no sense from an ecological point of view. It quickly became clear to me that we had to do something, »explains the energetic environmental scientist.
Six years later, the vision has become a reality: Librec AG has just opened the first industrial recycling factory for Switzerland's e-car batteries on the site of the former paper mill in Biberist. With a capacity of up to 12,000 tons per year, the complex is one of the largest in Europe. The emergence of numerous high -ranking industry representatives from the auto industry, science and politics also shows that the opening is “an event of national importance and international broadcast”.
Best quality in Europe
Over 97 percent of the starting materials such as cobalt, lithium, manganese, nickel, copper and aluminum are recovered from the cells of the old batteries that arrive from home and abroad in Biberist- a uniquely high rate worldwide. At the end of the recycling process, however, there are no new e-car batteries at Libec: «We only carry out the first step to recover the recycling materials. Our product that we sell to our European and Asian customers is the so -called black mass. » The quality of the grain -shaped recyclate is impressive how Jodok Reinhardt proudly explains: "Due to the very good feedback that we receive from our foreign partners, we can assume that we are currently producing the best black mass in Europe on the most attractive conditions and with maximum sustainability."
Sustainability plays a central role at LibreC AG: the industrial hall construction is largely made of wood, the roof of the factory is covered with solar cells, which means that the majority of the required energy can be covered. Even the residual energy stored in the old batteries, which must be unloaded in the system before further processing, is used for heating and operation. The EMPA certifies the recycling factory to have a battery material processed by other companies unmatched so far unmatched CO₂ footprint per tonne. Reinhardt's overarching goal: "Make e-mobility 100 percent sustainable."
Projects are planned abroad
At the beginning, Libec works with around 15 employees in laying operations. But soon the number of batteries, which are not used for use in the electric car or as an intermediate use as an energy storage, for example in photovoltaic systems-the so-called Second Life-. The company will then be able to increase the machine capacity and staff quickly and will reach the maximum 12,000 tons per year in three -shift operation. But Jodok Reinhardt is already thinking one step further: "We would like to become an attractive partner for collaborations abroad in the long term and, if everything runs according to plan, also check our own projects abroad. The ideas do not run out of the busy Solothurn for the time being - and if they do, the kitchen table is waiting at home.