How raw materials from millions of tons of e-car batteries are obtained
The Swiss company Libec would soon like to shred and recycle 10,000 tons of batteries per year in Biberist, and another 90,000 tons per year in Europe.
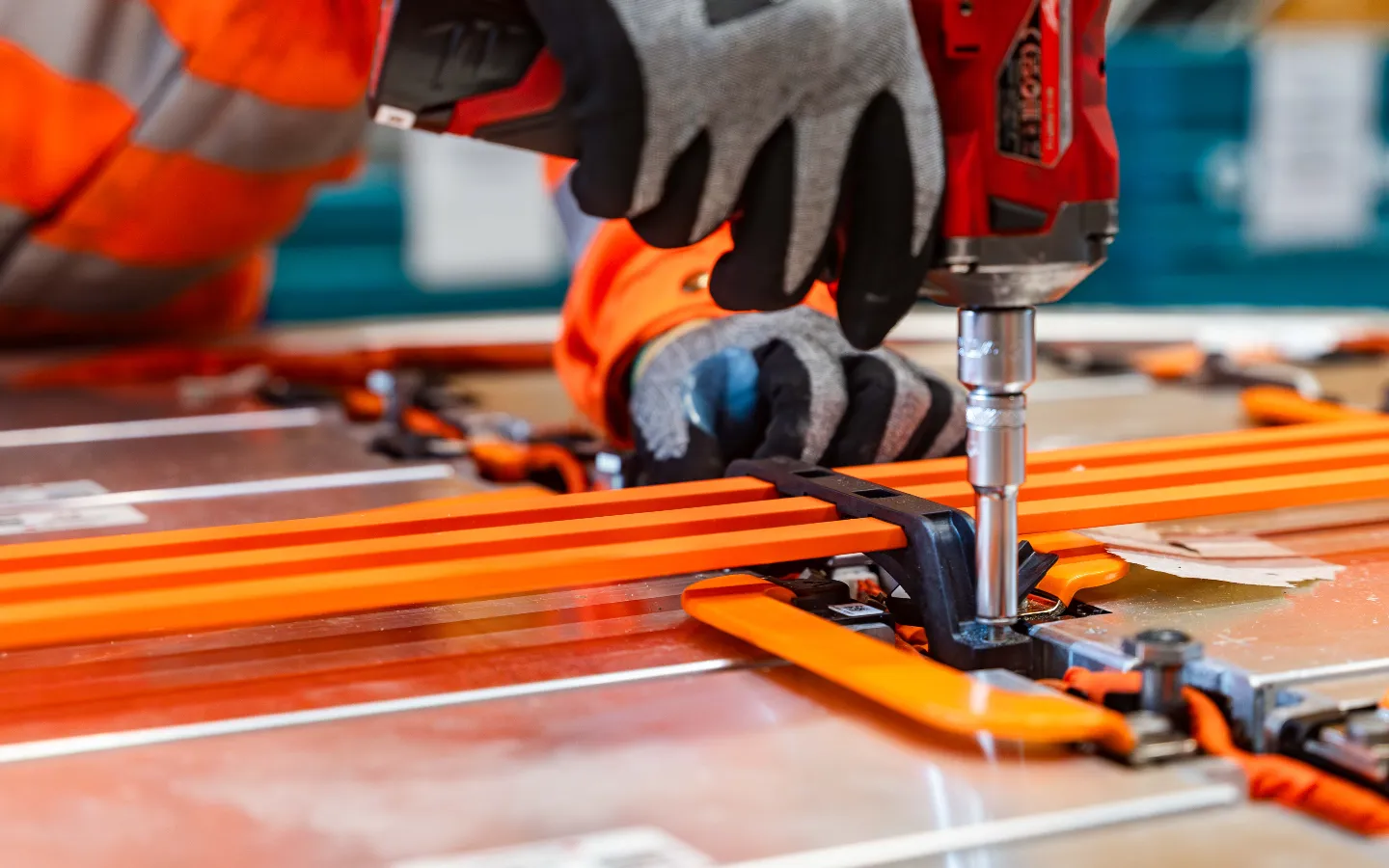
Tagesanzeiger - 02.01.2024 Joachim Laukenmann - E-car batteries provide raw materials: This is how recycling works | Daily Anzeiger
With electromobility, a million tons of challenge rolls towards us: the recycling of the lithium-ion batteries.
In 2023, around 1.5 million tons of new batteries for electromobility came on the street in Europe. But that's just the beginning. By 2030, the global need for lithium-ion batteries is likely to be more than versions today, a model calculation from the management consultancy McKinsey emerges.
"With 10 to 15 years of delay, the mass of batteries that have to be recycled increases," says Andrin Büchel from Technology and Society Lab of the Federal Material Examination and Research Institute (EMPA). "The increase is clearly dominated by the batteries for electric cars."
How big the dimension of the challenge is can be guessed at when you see a building that the Swiss company Libec is building on the site of a disused paper mill in Biberist near Solothurn. It is 150 meters long (as long as three Olympic swimming pools), 30 meters wide and twelve meters high. "From October 2024 we want to recycle 10,000 tons of e-car batteries per year," says Jodok Reinhardt, CEO from Libec. This corresponds to the mass of the Eiffel Tower annually and, according to Reinhardt's calculation, should cover the recycling requirement of large car batteries in Switzerland.
However, Libec is planning beyond Switzerland and would like to build a European network of battery collection points and recycling factories by 2026: In Central Eastern Europe and Southwest Europe, additional recycling capacities of around 90,000 tons per year are to be created.
The recycling process used by Libec can be followed step by step by walking from one side through the entire hall in Biberist. The first indoor part - like everyone else - is intended as an intermediate storage for incoming goods. The partner company Libatation is located in the second compartment. This initially checks which batteries can still be opened for a second life, for example for stationary memory to stabilize the power grid or in the area of mobility. Only those batteries that cannot be used further, hike to Libec into the third area.
High -voltage technicians will work there and unload the old batteries. The discharge current uses Libec and thus covers around a third of its electricity requirements for the system. The battery modules are opened in the fourth indoor part, partly by hand, partly automated. Cable connections and circuit boards are separated. The remaining battery modules wander into the heart of the system: the fully automatic production system worth a double -digit million amount.
This initially shreds the battery cells mechanically. Then various separation techniques follow with the help of vacuum, mechanical stress, air flows, seven and magnets. Everything takes place in a process isolated from the room air. "This is a high-tech process that we optimized without emissions," says Reinhardt. In the end, the main result is what is called black mass in the professional world: a powder that contains all important battery -specific raw materials and only very few contaminants.
According to Reinhardt, the LIBREC process is able to recycle more than 90 percent of the raw materials from the batteries, including cobalt, nickel, lithium, manganese, copper and also Grafit. Only the binders are lost. "We can regain the lithium that is important for batteries," says Reinhardt.
Chemical separation processes for recovery of the raw materials
But that's just the first step. In a second, the valuable materials contained in the black mass are prepared in such a way that new batteries can be made from them. However, this is not done by Libec, but, for example, by the Aurubis company based in Hamburg. Other large chemical and raw material companies such as BASF, Solvay and Umicore also specialize in the processing of the black mass.
A chemical separation process is usually used with the help of acids. In technical terms one speaks of hydrometallurgy. Only Umicore relies on pyrometallurgy: an energy -intensive method of metal extraction at very high temperatures and to exclude oxygen.
The EU stipulates that at least 50 percent and cobalt as well as nickel and copper must be recovered to at least 90 percent in the entire recycling process. The values continue to rise by 2032. As an incentive for recycling, the EU also stipulates the proportion of recycled raw materials in new batteries.
How do you get recycling most efficiently?
"It is a key question of how to get the collection of batteries and their recycling most efficiently and cheapest in Europe," says Reinhardt. The optimum looks like that there will finally be more than two dozen systems in Europe as in Biberist - but not all of LibreC.
Depending on the population and vehicle density, each of these systems in the vicinity of 500 to 1500 kilometers in diameter collects all e-car batteries and produces the black mass. In contrast to batteries, this can be transported safely and therefore cheaply. It is therefore worth driving the black mass to a handful of central large systems, where it is prepared for the production of new batteries.
Büchel from Empa sees a challenge for recycling in the changing chemical compositions of the battery cells: "Depending on the recycling processes, the recycling process must be adjusted." Today, nickel, manganese and the valuable cobalt are mainly used as cathode material. According to forecasts, iron will be increasingly being used in the cathode material in the future, so that such cell chemia gain the market share. "This cell chemistry is characterized by a lower intrinsic material value, which makes such batteries cheaper," says Büchel. "This makes your recycling less lucrative."
How the production of lithium-ion batteries and their recycling can be brought even better into an environmentally friendly cycle examine 11 Swiss research institutes and 24 industrial partners in Project Circubat. Libec and the Empa are also involved. The management of the project is located at the Center for Energy Storage of the Bern University of Applied Sciences.
A 2021 in the specialist magazine "Resources, Conservation and Recycling" published study It comes to the conclusion that recycling using hydrometallurgy releases 38 percent fewer CO₂ emissions than the breakdown of raw materials. "Since recycling does not cause landfills, it also reduces the pollution of soil, air and water compared to raw material reduction," says Reinhardt. "In addition, recycling gives us access to lithium, nickel, cobalt and other raw materials that are not available in Switzerland."
According to Reinhardt, recycling in Europe could deliver around 60 percent of raw materials that are required to produce new batteries for e-mobility. "That would reduce our raw material dependency."