Wie Rohstoffe aus Millionen Tonnen E-Auto-Batterien gewonnen werden
Die Schweizer Firma Librec möchte in Biberist SO bald 10’000 Tonnen Batterien pro Jahr schreddern und recyceln, in Europa weitere 90’000 Tonnen pro Jahr.
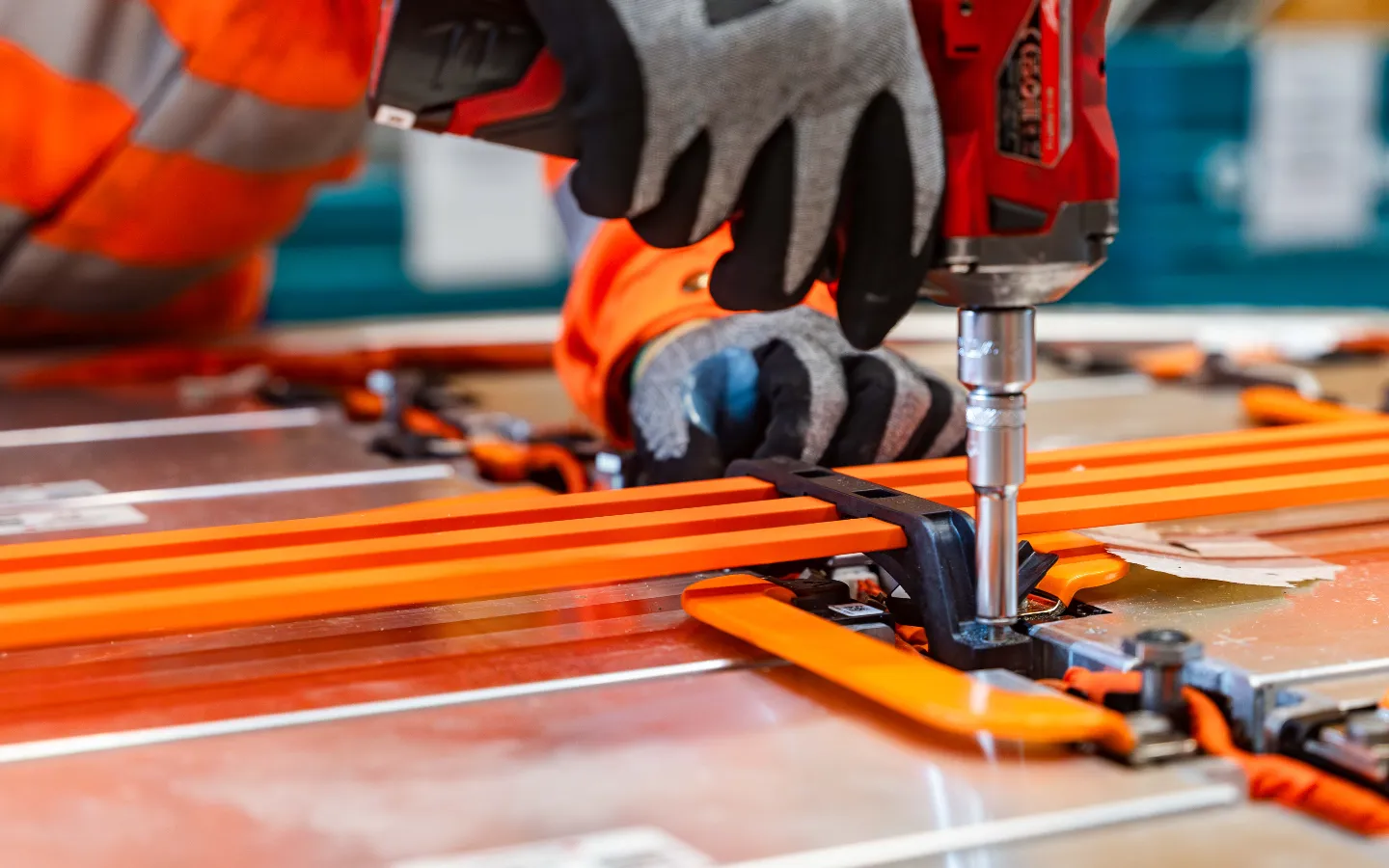
Tagesanzeiger - 02.01.2024 Joachim Laukenmann - E-Auto-Batterien liefern Rohstoffe: So funktioniert das Recycling | Tages-Anzeiger
Mit der Elektromobilität rollt eine Millionen Tonnen schwere Herausforderung auf uns zu: das Recycling der Lithium-Ionen-Batterien.
2023 sind in Europa rund 1,5 Millionen Tonnen neue Batterien für die Elektromobilität auf die Strasse gekommen. Aber das ist erst der Anfang. Bis 2030 dürfte sich der globale Bedarf an Lithium-Ionen-Batterien gegenüber heute mehr als versechsfachen, geht aus einer Modellrechnung der Unternehmensberatung McKinsey hervor.
«Mit 10 bis 15 Jahren Verzögerung steigt damit auch die Masse an Batterien, die recycelt werden müssen», sagt Andrin Büchel vom Technology and Society Lab der Eidgenössischen Materialprüfungs- und Forschungsanstalt (Empa). «Der Anstieg wird ganz klar von den Batterien für Elektroautos dominiert.»
Wie gross die Dimension der Herausforderung ist, kann man beim Anblick eines Gebäudes erahnen, das die Schweizer Firma Librec gerade auf dem Gelände einer stillgelegten Papierfabrik in Biberist bei Solothurn errichtet. Es ist 150 Meter lang (so lang wie drei Olympiaschwimmbecken), 30 Meter breit und zwölf Meter hoch. «Ab Oktober 2024 wollen wir hier 10’000 Tonnen E-Auto-Batterien pro Jahr recyceln», sagt Jodok Reinhardt, CEO von Librec. Das entspricht jährlich der Masse des Eiffelturms und sollte gemäss der Berechnung von Reinhardt den Recyclingbedarf an grossen Autobatterien in der Schweiz abdecken.
Librec plant aber über die Schweiz hinaus und möchte bis 2026 ein europäisches Netzwerk von Batteriesammelpunkten und Recycling-Fabriken aufbauen: In Mittelosteuropa und Südwesteuropa sollen zusätzliche Recycling-Kapazitäten von insgesamt rund 90’000 Tonnen pro Jahr entstehen.
Dem von Librec verwendeten Recycling-Prozess kann man Schritt für Schritt folgen, indem man von einer Seite durch die ganze Halle in Biberist läuft. Der erste Hallenteil – wie alle anderen noch unfertig – ist als Zwischenlager für ankommende Ware gedacht. Im zweiten Abteil ist die Partnerfirma Libattion angesiedelt. Diese prüft zunächst, welche Batterien sich noch für ein zweites Leben aufmöbeln lassen, etwa für stationäre Speicher zur Stabilisierung des Stromnetzes oder im Bereich der Mobilität. Nur jene Batterien, die sich nicht weiter nutzen lassen, wandern zu Librec in den dritten Bereich.
Dort werden Hochvolttechniker arbeiten und die Altbatterien entladen. Den Entladungsstrom nutzt Librec und deckt damit rund ein Drittel seines Strombedarfs für die Anlage ab. Im vierten Hallenteil werden die Batteriemodule geöffnet, teils von Hand, teils automatisiert. Kabelverbindungen und Leiterplatten werden separiert. Die verbleibenden Batteriemodule wandern ins Herzstück der Anlage: die vollautomatische Produktionsanlage im Wert eines zweistelligen Millionenbetrags.
Diese zerkleinert die Batteriezellen zunächst mechanisch. Dann folgen verschiedene Trenntechniken mithilfe von Vakuum, mechanischer Beanspruchung, Luftströmen, Sieben und Magneten. Alles erfolgt in einem von der Raumluft abgeschotteten Verfahren. «Das ist ein von uns optimierter Hightech-Prozess gänzlich ohne Emissionen», sagt Reinhardt. Heraus kommt am Ende vor allem das, was in der Fachwelt als Schwarzmasse bezeichnet wird: ein Pulver, das alle wichtigen batteriespezifischen Rohstoffe und nur noch sehr wenige Verunreinigungen enthält.
Laut Reinhardt ist es mit dem Prozess von Librec möglich, mehr als 90 Prozent der Rohstoffe aus den Batterien zu recyceln, darunter Cobalt, Nickel, Lithium, Mangan, Kupfer und auch Grafit. Verloren gehen nur noch die Bindemittel. «Das für Batterien wichtige Lithium können wir zu mehr als 97 Prozent zurückgewinnen», sagt Reinhardt.
Chemisches Trennverfahren zur Rückgewinnung der Rohstoffe
Das ist aber nur der erste Schritt. In einem zweiten werden die in der Schwarzmasse enthaltenen Wertstoffe so aufbereitet, dass daraus neue Batterien gefertigt werden können. Das wird allerdings nicht von Librec geleistet, sondern zum Beispiel von dem in Hamburg ansässigen Unternehmen Aurubis. Auch andere grosse Chemie- und Rohstoffunternehmen wie BASF, Solvay und Umicore spezialisieren sich auf die Verarbeitung der Schwarzmasse.
Dabei kommt meist ein chemisches Trennverfahren mit Hilfe von Säuren zum Einsatz. In der Fachsprache spricht man von Hydrometallurgie. Nur Umicore setzt auf Pyrometallurgie: ein energieintensives Verfahren der Metallgewinnung bei sehr hohen Temperaturen und unter Ausschluss von Sauerstoff.
Die EU schreibt vor, dass beim gesamten Recycling-Prozess bis ins Jahr 2028 Lithium zu mindestens 50 Prozent und Cobalt sowie Nickel und Kupfer zu mindestens 90 Prozent zurückgewonnen werden müssen. Bis 2032 steigen die Werte weiter an. Als Anreiz für das Recycling schreibt die EU ebenfalls vor, zu welchem Anteil recycelte Rohstoffe in neuen Batterien zum Einsatz kommen müssen.
Wie kriegt man das Recycling am effizientesten hin?
«Es ist eine Schlüsselfrage, wie man europaweit die Sammlung der Batterien und deren Recycling am effizientesten und günstigsten hinkriegt», sagt Reinhardt. Das Optimum sieht wohl so aus, dass es in Europa schliesslich mehr als zwei Dutzend Anlagen wie in Biberist geben wird – allerdings nicht alle von Librec.
Je nach Bevölkerungs- und Fahrzeugdichte sammelt jede dieser Anlagen in der Umgebung von 500 bis 1500 Kilometern Durchmesser alle anfallenden E-Auto-Batterien ein und stellt die Schwarzmasse her. Diese lässt sich im Gegensatz zu Batterien gefahrlos und somit günstig transportieren. Daher lohnt es sich, die Schwarzmasse zu einer Handvoll zentraler Grossanlagen zu fahren, wo sie für die Herstellung neuer Batterien aufbereitet wird.
Eine Herausforderung für das Recycling sieht Büchel von der Empa in den sich ändernden chemischen Zusammensetzungen der Batteriezellen: «Je nachdem müssen die Recyclingverfahren angepasst werden.» Heute kommen als Kathodenmaterial hauptsächlich Nickel, Mangan und das wertvolle Cobalt zum Einsatz. Gemäss Prognosen wird künftig zunehmend Eisen im Kathodenmaterial verwendet, sodass solche Zellchemien an Marktanteil gewinnen. «Diese Zellchemie zeichnet sich durch einen geringeren intrinsischen Materialwert aus, was solche Batterien günstiger macht», sagt Büchel. «Dadurch wird ihr Recycling allerdings weniger lukrativ.»
Wie sich die Herstellung von Lithium-Ionen-Batterien und deren Recycling noch besser in einen umweltfreundlichen Kreislauf bringen lassen, untersuchen 11 Schweizer Forschungsinstitute und 24 Industriepartner im Projekt Circubat. Auch Librec und die Empa sind beteiligt. Die Leitung des Projekts liegt beim Zentrum für Energiespeicherung der Berner Fachhochschule.
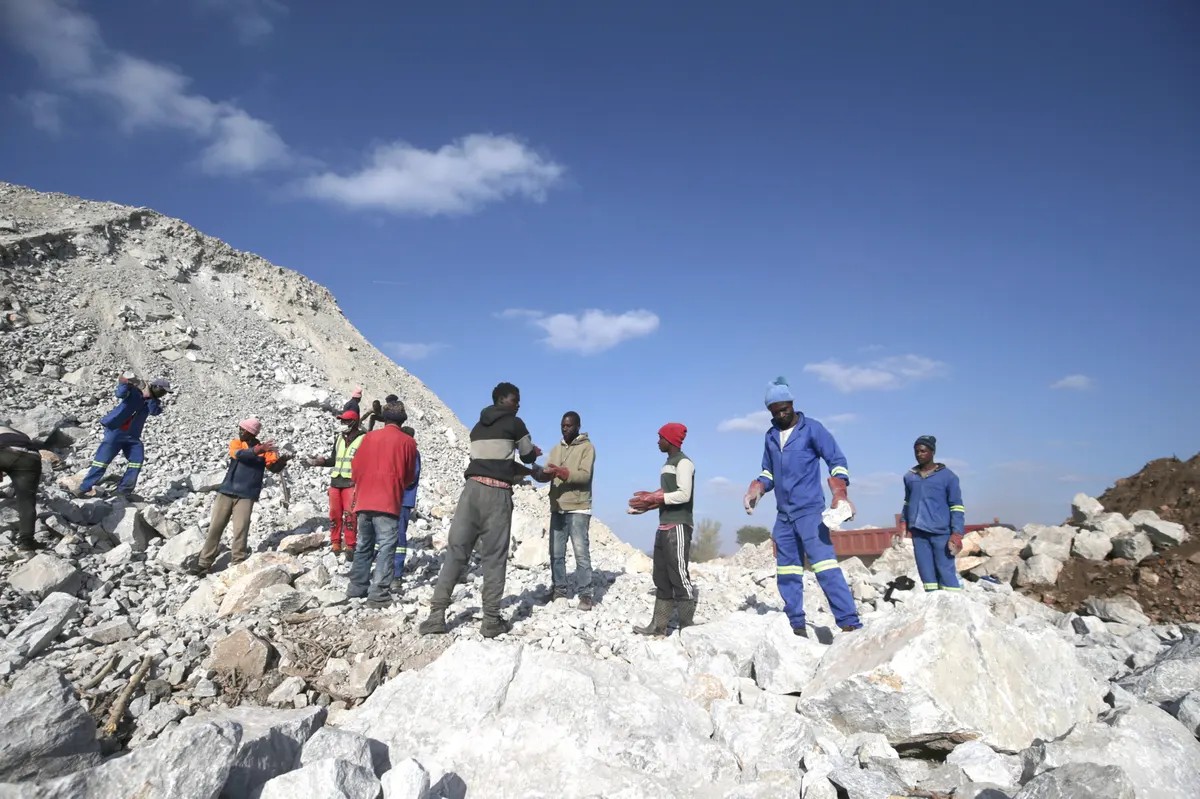
Eine 2021 im Fachmagazin «Resources, Conservation and Recycling» publizierte Studie kommt zum Schluss, dass Recycling mittels Hydrometallurgie 38 Prozent weniger CO₂-Emissionen freisetzt als der Abbau von Rohstoffen. «Da Recycling keine Deponien verursacht, reduziert es gegenüber dem Rohstoffabbau auch die Verschmutzung von Boden, Luft und Wasser», sagt Reinhardt. «Zudem verschafft uns das Recycling Zugang zu Lithium, Nickel, Cobalt und anderen Rohstoffen, die in der Schweiz nicht zur Verfügung stehen.»
Um 2050 könnte das Recycling in Europa laut Reinhardt rund 60 Prozent der Rohstoffe liefern, die für die Herstellung neuer Batterien für die E-Mobilität benötigt werden. «Das würde unsere Rohstoffabhängigkeit reduzieren.»